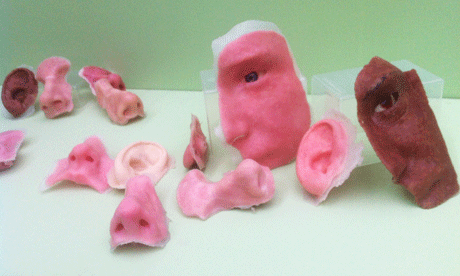
A giraffe wearing a frilly ruff, an Escher-like puzzle of interlocking cogs and a homoerotic Batman figurine are just some of the strange items on display at the 3D Printshow in London this week, a trade fair which proves that where high technology goes, novelty trinkets follow. But wade through the endless booths promoting plasticky tat and you'll find one of the most worthwhile applications of 3D-printing to be developed yet.
At first it looks like something from a joke shop: a shelf displays a neat line of rubber noses, available in every imaginable skin tone, and a small pile of eyes. There are ears, too, and half a face.
"We originally bought a 3D-printer to make quick models of product ideas in the office," says their creator, industrial designer Tom Fripp. "Then the University of Sheffield got in touch a few years ago, asking if it would be possible to print something resembling soft tissue."
The result, after several years of collaborative research and prototyping in partnership with the University and the Wellcome Trust, is the first series of 3D-printed prostheses.
"Conventional maxillofacial prosthetics are incredibly laborious and expensive to produce," says Fripp. "You have to take an impression from the area of trauma, cast a plaster positive, then make a mould, carve the desired form in wax, and cast it in silicone. The end result of this handmade process costs between £1,500 to £3,000."
With digital modelling technology, it can be quicker, cheaper – and much more accurate. Fripp's company have developed a process in which the patient's face is 3D-scanned, avoiding the need for a sometimes painful and invasive impression, and the specific contours then added to a digital model of the new prosthetic part, to create a perfect fit every time. The parts themselves can be scanned from other people or replicated from the patient's own physiognomy – one ear can be scanned and mirrored to replicate another.
"We have a whole bank of different noses and ears now," says Fripp. "One lady had always admired her friend's nose, so we made her one just like it."
The parts are 3D-printed in full colour in starch powder, forming a lightweight model that is then vacuum-infiltrated with medical grade silicone, binding it together and providing durable flexibility. The first prosthesis costs around the same as the traditional process, but once the digital model has been made, successive parts can be produced for around £150.
"Prostheses do tend to wear out and degrade after exposure to water, sun and daily wear and tear," says Fripp. "But 3D-printed prostheses allow for different options – for example if you get a sun-tan, you can just email us about your new skintone and we'll print you a new one."
The target market for which the project was developed, he says, is the developing world, where prosthetic skills are often in short supply. The main barrier at present is the prohibitive cost of 3D-scanning technology, but with prices coming down, the availability of low-cost, individually-customised prostheses could soon be a reality.
